My wonderful wife put together a crafting party where we customized clothes with her vinyl cutter. I’m currently obsessed with Splatoon, so I used it as an opportunity to make a Grizzco-themed hoodie.
I started by loading up the game and taking some screenshots in order to create silhouettes of the game assets. I grabbed one in the Grizzco lobby on a day when my favorite gun happened to be in rotation, one from the “Grizzco Industries Occupational-Safety Guidelines,” and one of the results screen after a match.
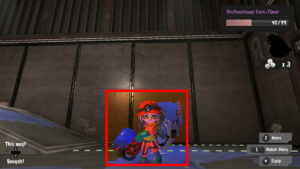
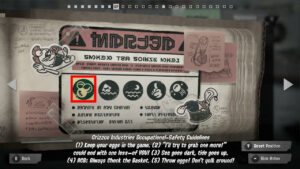
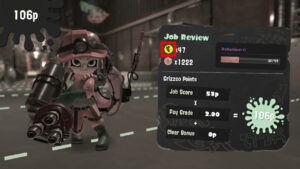
I also found images online of a Grizzco logo the squid icon, both of which I think are fan-made but the site I found them on did not provide information that would allow me to attribute the creator.
I used GIMP to extract the regions of the images I cared about, transform them as-needed, and arrange them tightly in a square to save material. With the image flattened and the non-transparent content selected, I used the selection to path tool and exported the outline path as an SVG image for the Cricut software to read.
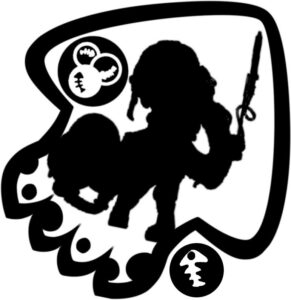
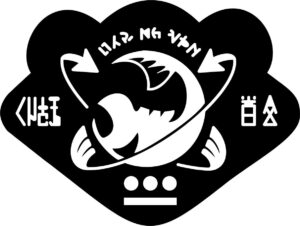
Yani used the Cricut machine to cut the patterns out of sublimation ink sheets, as well as a bunch of vinyl pieces that she designed. I wanted to use these particular sheets to get a splatter effect in the final pattern.
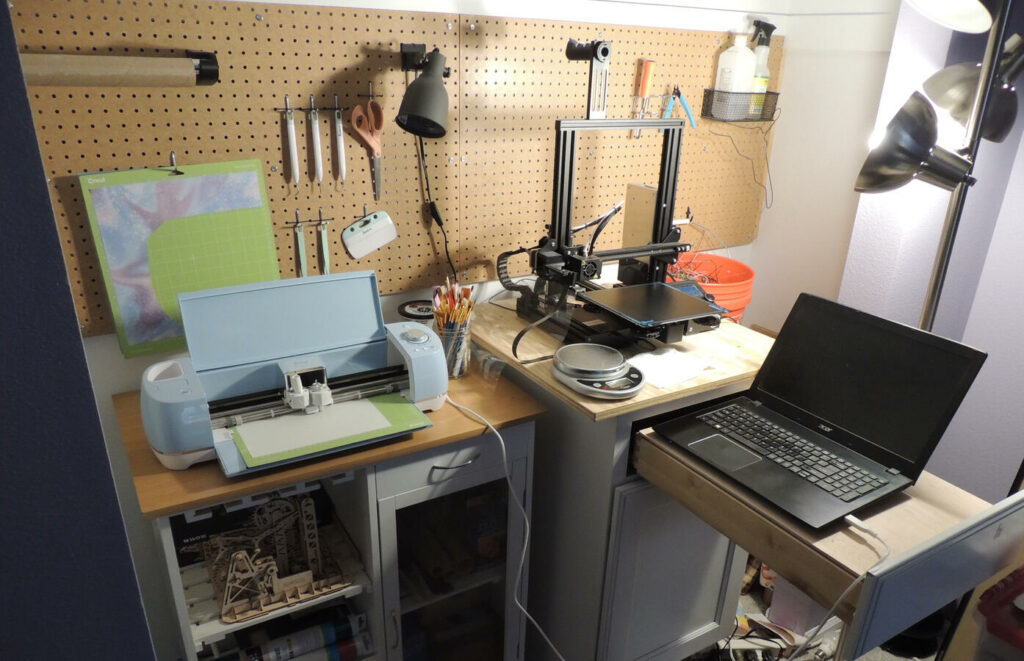
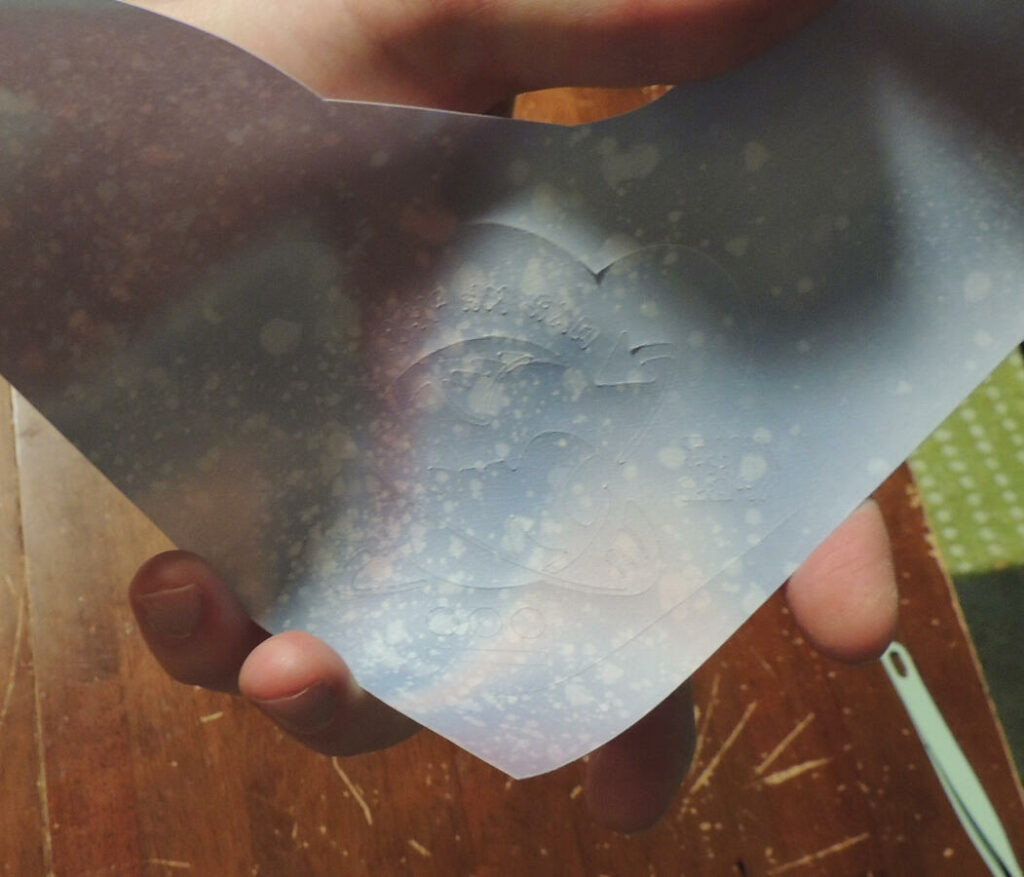
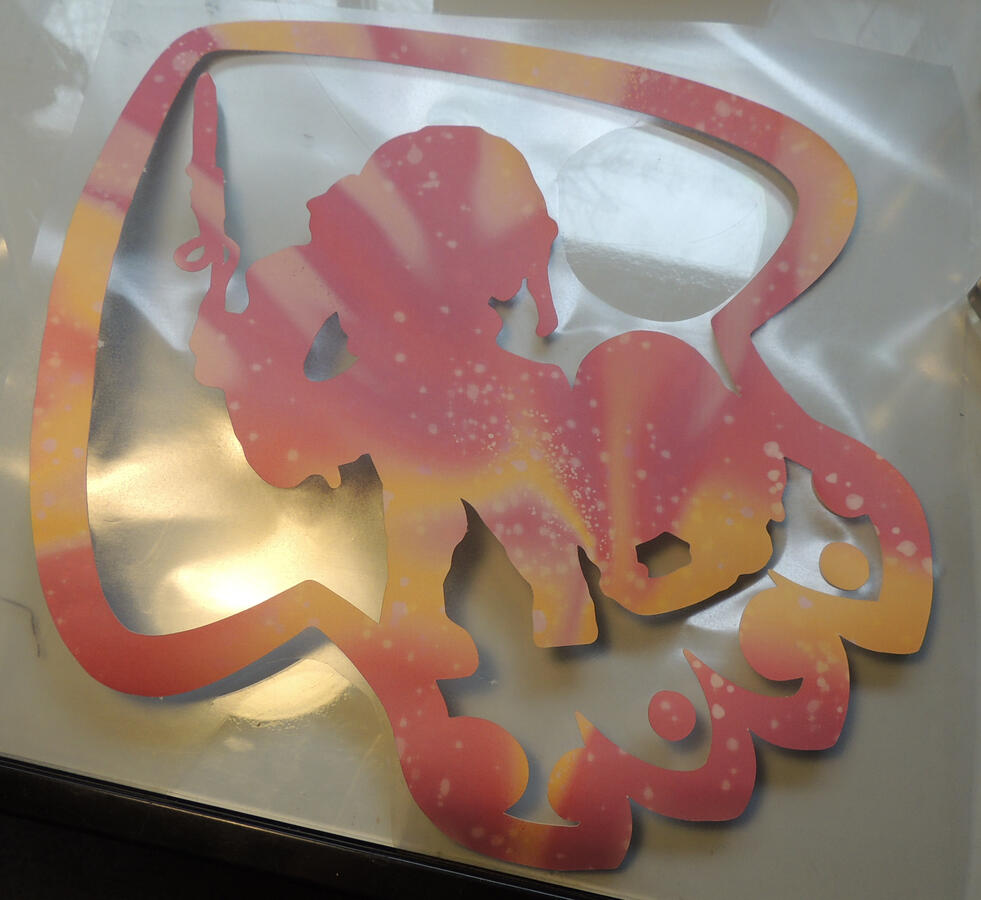
The ink on the sheets transfers to a polyester fabric when heated to around 200 degrees Celsius. Cricut sells a heating machine with a big flat plate to heat a large area to the right temperature, but it can also be done pretty well with a regular clothes iron. Since our clothes iron just has cloth settings and not temperature graduations, I used a thermal camera to dial in the temperature setting for the iron.
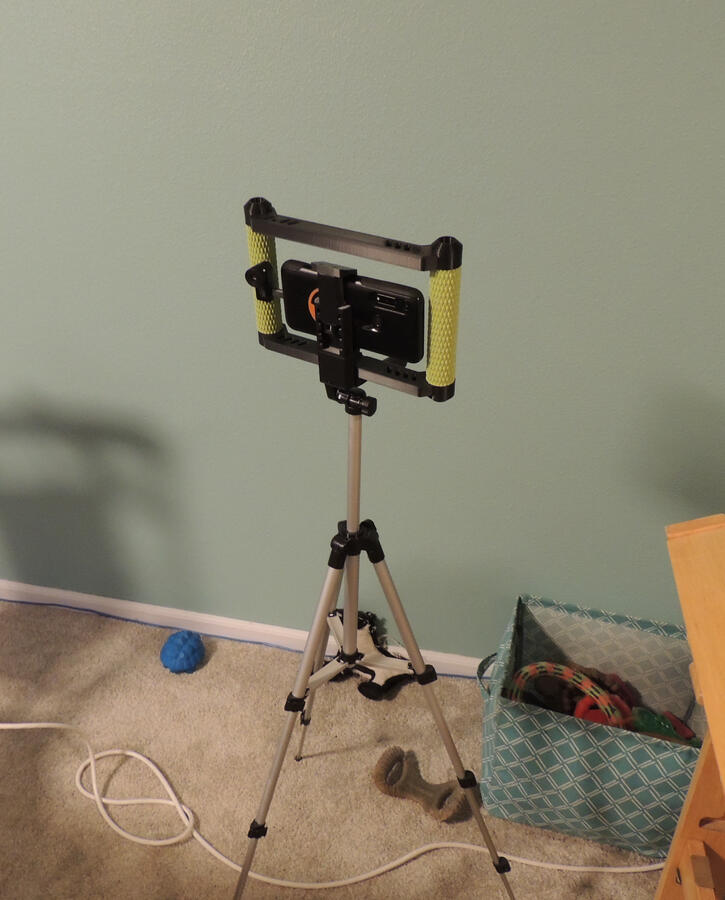
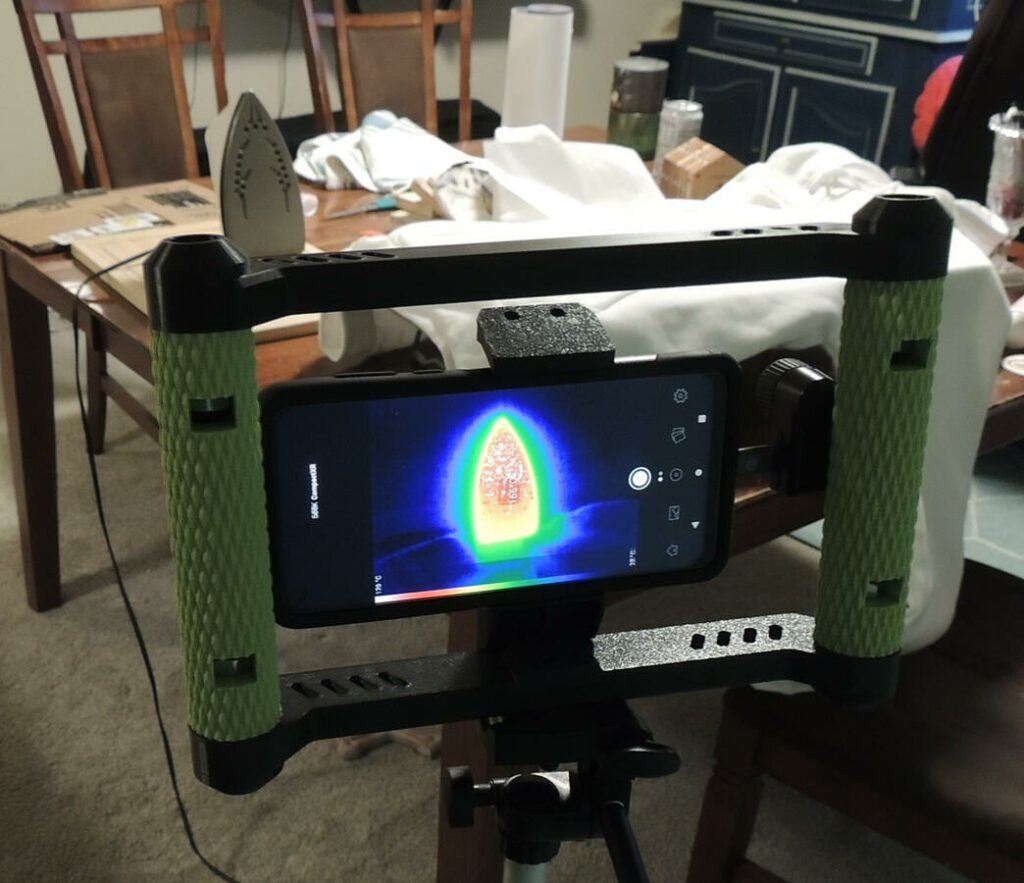
Following instructions we found for the Cricut transfer sheets, I used the iron to heat the ink sheets for about a minute to transfer the ink, lifting the iron in between locations. The smaller patches were more successful, and if I were to do this again I would not lift the iron.
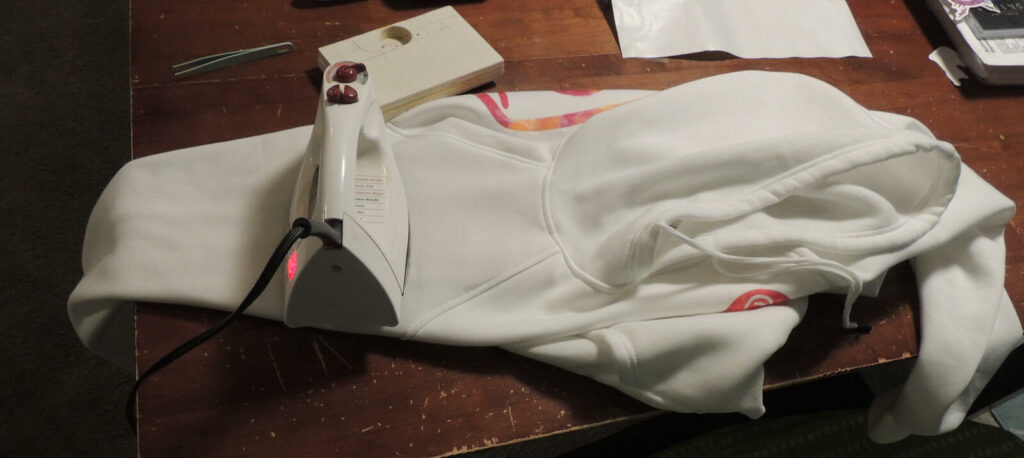
Lifting the iron to move it is supposed to prevent you from dragging the ink sheet when you drag the iron, but there isn’t much chance of that happening as long as you put a piece of parchment paper in between the iron and the ink sheet. The problem is that lifting the iron can allow the ink sheet to lift up where it has heated and warped, which can cause parts of the pattern you haven’t heated yet to move, especially right near the edge of the iron where it can leave small lines.
This caused a misalignment of some parts of my largest pattern of about a quarter inch. It’s barely noticeable, but next time I will try some other approaches to keep this from happening, or else stick to patterns around the size of the iron.
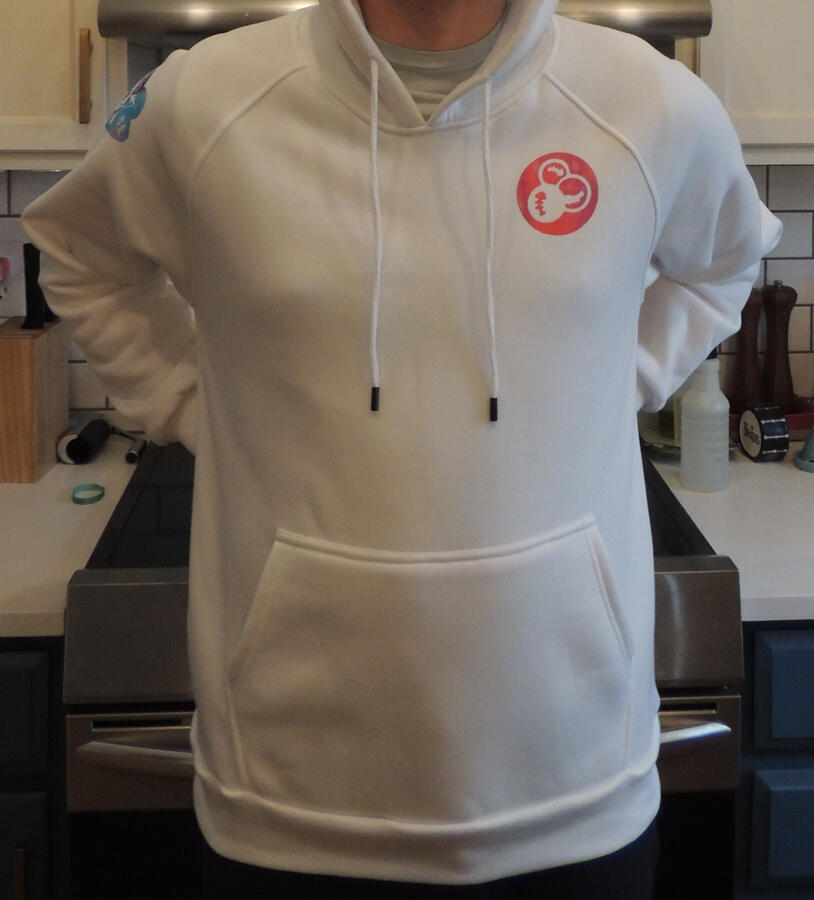
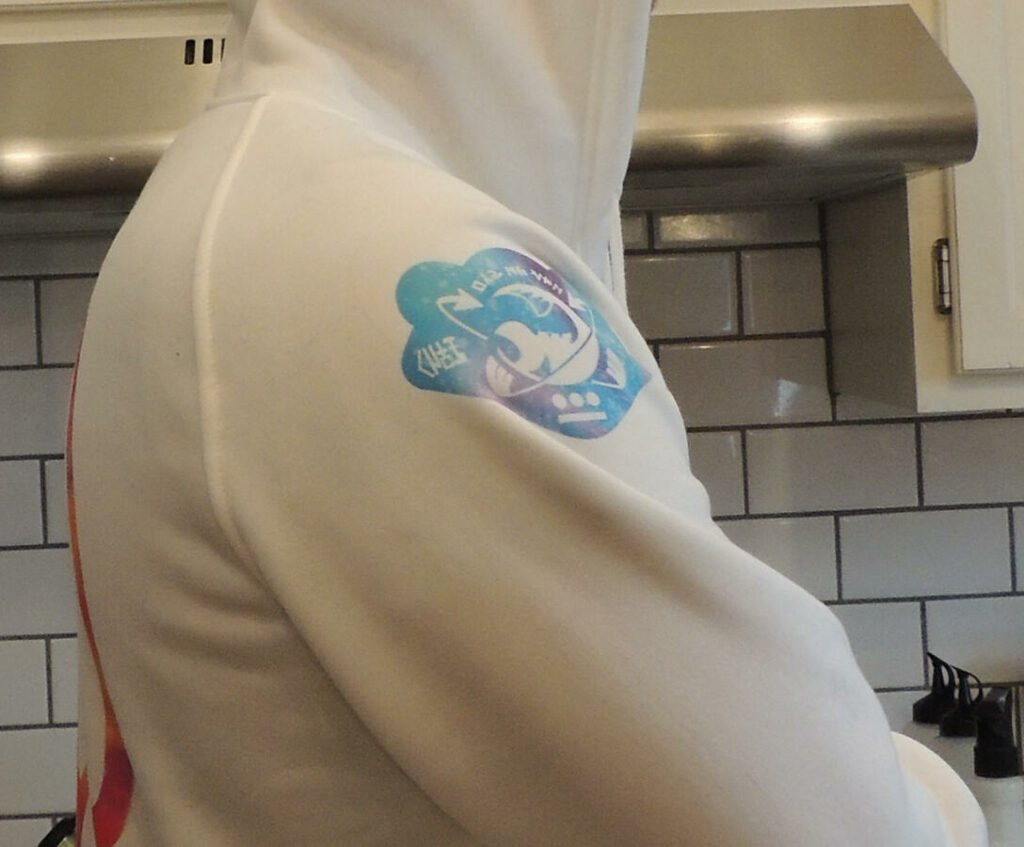
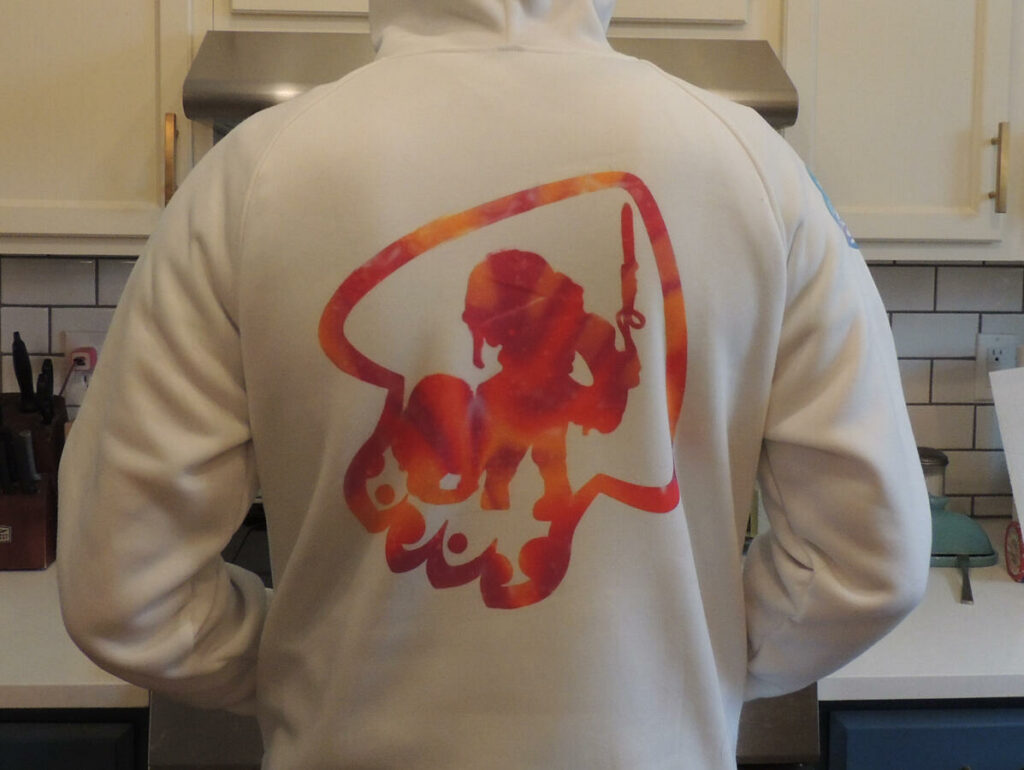
I applied a total of 3 iron-on patches to this sweater, and I’m really happy with the results, even after washing it with cold water. I would highly recommend this approach for decals on polyester fabric.